Cyma Builders has recently completed a three phase upgrade to Lonza’s Powder Media Suite in Walkersville, MD. The upgrades were designed to provide GMP compliance, improved flows and overall optimization of the area to support Lonza’s manufacturing operations. Click here for more details and finished project photos!
Lonza’s existing powder media suite required upgrades to achieve cGMP standards in order to continue manufacturing product. Improvements looking to be gained included improvement of process flow, congestion relief, crease facility capacity, Provide EU/FDA Compliant layout and environment and provide EU compliant airlocking. This project was scheduled for three phase in order to accommodate ongoing operations.
Phase 1 included installation of new airlocks and high speed roll up doors to properly segregate the Powder suite. Additionally, the walls of the existing room were lined with heat welded takiron and a new epoxy floor installed to provide GMP finishes throughout the suite. Completing the finish work was particularly difficult due to the existing utilities exposed within the room that could not be removed (or recessed) without adding substantial cost to the project. New ductwork was installed during this phase to prep for connection to a new AHU to be installed under the future phases. New suites were also constructed to house pre-blending operations and a relocated CIP skid.
Phase 2 included installation of new Material & Personnel Airlocks, Chemical Storage and Weigh/Dispense Suite. The Weigh/Dispense Suite was purpose built with multiple down flow booths to accommodate specific products and personnel protection. Finishes within the Phase 2 suites matched those installed under Phase 1, including takiron walls, epoxy floors and epoxy painted ceilings. Additionally, a new 15,000 CFM AHU was installed during this phase to provide the necessary air changes to accommodate the program. The AHU installation included rooftop dunnage and platforms, along with new plant utility distribution.
Phase 3 included demolition of the existing Weigh/Dispense Suite, replaced by the Phase 2 suite. This area was then converted to a Chemical Staging and Personnel In Airlock. The finishes in Phase 1 &2 were carried through to Phase 3, and the new HVAC system was extended and leveraged to provide the appropriate air changes.
Once Phase 3 was complete, the Powder Media Suite was compliant with cGMP standards, achieved uni-directional flow and was operationally optimized for the program going forward. The project was completed on time and within budget.
Cyma Builders recently completed construction on a 10,000 SF facility for Biocoat in Horsham, PA. Biocoat and their new facility were recently featured in Philadelphia Business Journal. Check it out!
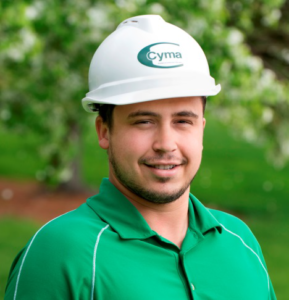
One of Cyma Builders & Construction Managers’ up and coming Superintendents, Erik Settelen, successfully passed the Board of Certified Safety Professionals (BCSP), Safety Trained Supervisor in Construction (STSC) Exam on March 1st, 2017. The STSC is a nationally recognized third party safety certification for those with supervisor responsibilities in construction. In the past twenty years, the responsibilities of safety professionals have expanded. Safety issues have become more complex and today’s safety professionals must be continually better qualified. BCSP credential holders are among the most highly trained, educated, and experienced individuals in the safety field. Currently, the BCSP has only 6,000 individuals who actively hold STSC certification.
Erik has been a Carpenter and Superintendent with the Cyma Builders & Construction Managers for 3 years and a member of the Local 167 and local 1462 Northeast Regional Council of Carpenters for 6 years. Mike Royce, Sr. comments, “Erik is very interested in safety and shows this on a daily basis, he is proactive with the pre-task safety planning effort and is very helpful in completing our client’s Safe Permits to Work, he has reached out to contractors in a positive way that has produced better JSAs earlier in the process.” Mike Royce, Sr. is a Construction Safety Specialist supporting the projects and sites that Erik supervises.
Cyma Builders was selected by Becton Dickinson as their construction management partner to complete a comprehensive Master Plan renovation of two (2) sites, their corporate headquarters in Franklin Lakes, NJ and a manufacturing facility in Sparks, MD. This project was designed to be a multi-year effort to strategically renovate each facility, while strategically utilizing swing space and maintaining daily business operations throughout each campus. The end goal was to modernize the workplace by converting traditional office space to a more open, collaborative and flexible environment.
In Franklin Lakes, the initial C2 renovation (left) was chartered as a pilot to construct numerous flexible office features to assist in evaluation of those that would truly be functional for BD. The existing C2 area was 12,000 SF consisting of an antiquated conference facility. The existing space was gutted back to an open floor plate, which included removal and infill of an existing elevator shaft. The new program consisted primarily of open office layout with sit-to-stand workstations, but also include private offices for high-level associates, conference rooms, huddle rooms, privacy rooms and hoteling space. A new employee training room was also programmed to accommodate large training sessions, and included modern fold partition flexibility to segregate the space into smaller areas. The space required upgrades of the existing HVAC distribution to accommodate the office layout, including new VAV’s/reheat coils and low pressure duct distribution and GRD’s. Power was distributed in the 1st floor plenum and cored through the 2nd floor slab to accommodate the workstation layout. A robust AV package was installed throughout all conference and collaboration space, including flat screen monitors, wireless projection systems and video conferencing capabilities. To increase mobility, unassigned workstations were deployed with lockers to accommodate those employees who chose to work from home more frequently. This portion of the project was completed on time and under budget with positive reviews from the associates who occupied the area.
Cyma Builders and Construction Managers were retained by DPT Laboratories to construct a new small volume parenteral (SVP) manufacturing suite and a new compounding suite at their Lakewood, NJ facility. The project was part of an ongoing master plan being executed at the facility that involves constructing individual SVP suites to fulfill the CDMO needs of their various clients
The 7,200 SF clean room was constructed to GMP EU classification and within the footprint of an active cGMP manufacturing facility. At the onset of the project, Cyma had to take extensive precautions to ensure the construction activities would not affect the active pharmaceutical manufacturing operations that were being conducted directly adjacent to the new suite. These precautions included clean room temporary partitions, strategic placement of negative air machines to ensure the control of dust and maintain pressure, as well as a diligent clean up effort to ensure that no dust or construction debris migrated into the plant. Cyma was also directly responsible for the flow of the contractors on site and ensuring they did not deviate from approved egress pathways. The FDA, EU, and DPT’s clients conducted several routine and surprise audits during construction without having a single observation that could be attributed to the construction team.
The overall construction included a modular clean room system for all clean room walls, ceiling and doors. This system was to be integrated into the existing adjacent suite that used the same modular system. Since the existing suite was in production 7-days a week, Cyma had to perform the tie-in to the suite during a previously scheduled bi-yearly shutdown. Cyma successfully completed five separate integration points at this shutdown, when the overall suite construction was only approximately 35% complete. Using the aforementioned clean room temporary partitions, Cyma was able to ensure that the existing suite was adequately sealed and protected while the rest of the suite was completed. The suites also had a trowel applied epoxy floor system with integral cove base.
The project had a significant amount of support infrastructure. This included two custom AHU’s, a new process and HVAC chilled water system, as well as a custom AWFI heat exchanger skid for an AWFI sub-loop that was being installed as part of the project. These systems were also tied in to the existing systems already in service at the plant. Cyma worked with the engineering and production teams at the plant to schedule strategic shutdowns to allow the project to maintain schedule while almost completely negating the impact to production.
The infrastructure was installed on a new two story rooftop/internal mezzanine platform system that was constructed immediately above the process space. This platform was independently supported from the existing structure. It is important to note that Cyma also worked with the design team to ensure that this platform was completely walkable and unobstructed by any of the ductwork, piping, or other utilities being installed to support the suite below.
At 60% completion, Cyma was informed that the customer purchased filling line was approximately 4 months behind schedule. This delay proved devastating to the client’s overall schedule to get the suite into active production by the end of 2016. In order to help their client achieve their goal, Cyma worked with their critical subcontractors to revise the sequence of construction to minimize this impact. This allowed almost 80% of the suite to be constructed while the filling line was being completed. Once the filling line arrived, Cyma rigged the unit into place as quickly as possible so the rest of the suite could be completed. Cyma then connected all of the relevant utilities and supported the startup of the filling line.
Cyma Builders has recently broken ground on a Flavors Facility Expansion for Symrise in Branchburg, NJ. The 5 story building addition will accommodate a new spray dryer and provide approx. 20,000 SF of space to accommodate operational requirements. Follow our progress live on our webcam!
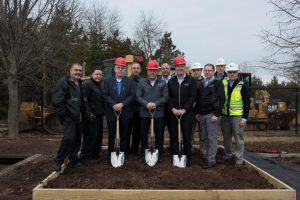
Cyma Builders & Construction Managers announced a safety certification achievement for one of their Superintendent’s, Paul Hahr. On April 21, 2016 Paul passed the Board of Certified Professionals (BCSP) Safety Trained Supervisor in Construction certification. The STSC is a nationally recognized third party safety certification for those with supervisor responsibility in construction.
Paul Hahr has been with Cyma Builders & Construction Managers since 2011 and has displayed an incredible reputation among his clientele as well as his fellow employees. Tom Santoli, Director of Safety and Health for Cyma stated, “Paul Hahr is a diligent and experienced Superintendent that understands and embraces the critical role that site supervision plays in the construction safety effort. Paul has repeatedly demonstrated his ability to proactively identify safety and health challenges on complicated pharmaceutical construction projects and his skill implementing safety solutions in the field.”