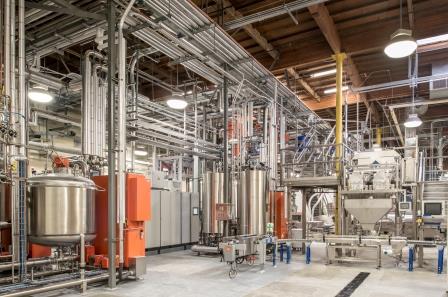
Mogul #3 Installation
The Mogul #3 Installation consisted of three major areas of new construction: installation of a new production line, exterior equipment installation and interior equipment installation and infrastructure upgrades. All three areas were constructed while the existing facility remained in operation with no disruption except for an essential shutdown. A 36 hour site wide shutdown was necessary to perform load shedding from existing switchboards to newly furnished and installed switchboards to feed the new production line. The shutdown required coordination between two other tenants at the facility and tie-ins to existing product lines, compressed air, clean steam, natural gas and cooling water. New air compressors, dryers, filters and receiver tanks were installed as part of the facility upgrades.
New underground plumbing and footings were installed inside an existing warehouse space to support the new production line. A stainless steel platform was erected to house new production and packaging equipment. The receiving, rigging and setting of equipment purchased from vendors in the Netherlands and Australia was managed by Cyma and coordinated with onsite technicians. The equipment was carefully installed and precisely leveled according to the manufacturers requirements. A total of seven prefabricated, environmentally controlled rooms were constructed, each complete with an automated track system that communicated with the rest of the production equipment. Several layers of intricate process piping served the new equipment and an array of interconnecting piping, conduit, ductwork and controls were heavily coordinating to achieve a fully functional system while meeting the end users spatial and sanitary requirements. Product conveying lines, inspection stations and packaging lines were also installed as part of the final stages of the process.
New exterior equipment pads were required for new boilers, cooling tower, air handling unit, storage silo and associated equipment to meet the demands of the new production line. All of the equipment was received, rigged, set and installed by Cyma. Power and utilities to this equipment required structural supports secured to the side of the existing facility and ran approximately 300 ft. from the existing boiler room to the new equipment pad.